Beyond Compliance: Why the Future Homes Standard should be a Starting Point, not the Finish Line
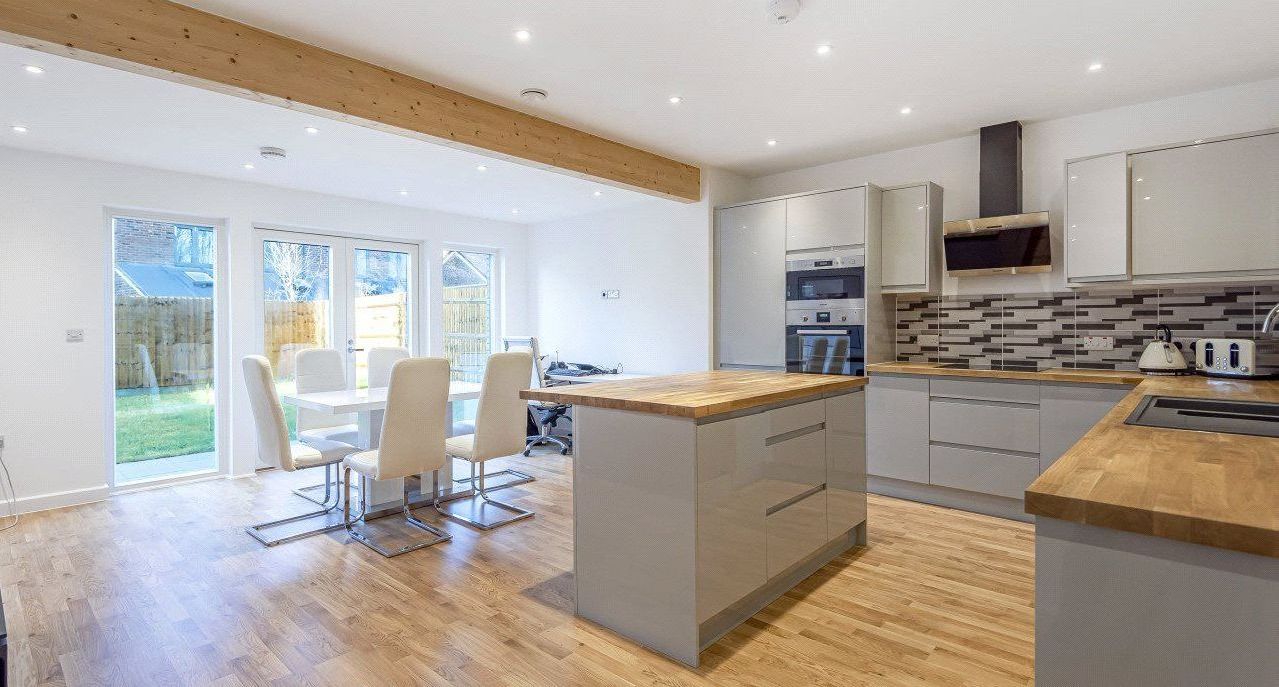
Dr Anthony Greer, Corporate Strategy Director of offsite housing specialists TALO, looks at why the Future Homes Standard represents a welcome move in the right direction for improving the energy performance and sustainability of new homes. He also considers why it feels more like catching up than moving ahead.
The final specifications for the new Future Homes Standard, including the implementation date, are set to be announced this year. The aim is to decarbonise new homes in England by improving the energy efficiency of heating and hot water systems and by significantly reducing heat loss.
The ambition is really positive and very welcome. However the gap between where the regulations are heading and what some housebuilders and developers are already achieving using advanced offsite technology is growing. Many architects and building designers already feel that whilst the new regulation will make a difference and is a step in the right direction, it is behind where it should be.
From Building Regulations to Better Buildings
Current regulations under Building Regulations Part L permit air permeability levels up to 10m³/hr/m², with the notional model assuming 5m³/hr/m². The Future Homes Standard is expected to demand levels closer to 3m³/hr/m², which is still a long way short of the Passivhaus benchmark of 0.6 m³/hr/m².
However, for developers still relying on traditional site-based construction methods, meeting the new threshold will be challenging and will incur additional cost. And this is at a time when skilled labour is still in short supply, build quality can vary from site to site, and achieving consistency, especially at scale, is very difficult.
The impact for traditional housebuilding? Increased risk. Risk of non-compliance. Risk of cost and programme overruns. Risk of reputational damage. And ultimately, risk of failing to meet homeowner expectations for higher energy performance and lower running costs.
In contrast, what can be seen as a challenging increase in building performance for traditional housebuilding, can also be viewed as an underwhelming level of performance when buildings constructed using offsite manufacturing technology can go much further.
There is a huge opportunity for offsite systems to deliver homes which significantly exceed the new Future Homes Standard on energy performance – as well as achieve on time/on budget delivery and at the same time being cost competitive with traditionally constructed homes.
The Housebuilding Sector can Go Further but Regulation isn’t Keeping Up
If the goal is to reduce energy demand and futureproof new housing, we need regulation that reflects what is already technically and economically feasible. And in some cases, that means looking beyond the UK.
In Finland, where around 70 per cent of all new housing is built using offsite manufacturing, energy performance standards have long exceeded those proposed under the new Future Homes Standard. TALO’s offsite timber superstructure system, for example, has been developed and proven for climate extremes as low as -50. It is now being used in the UK to deliver homes that exceed Passivhaus air tightness levels as standard and with no cost premium.
This advanced timber superstructure system is a model that shows what’s possible when quality, consistency and energy performance are embedded into the construction process from the outset.
The challenge for UK housebuilding is not that we lack the solutions, it is that we lack the regulatory urgency to adopt them at scale.
A Long Timeline for Change – and Why that’s an Issue
The fact that new homes may not need to meet the new standards until the end of 2026 raises serious concerns. In the context of rising energy prices, a housing crisis, ever tighter margins, and growing consumer demand for more sustainable living, this delay feels like a missed opportunity.
Every year we wait is another year of delivering homes that could – and should – perform better. Not to mention reduce environmental impact in the climate crisis. And for residential property developers, it’s another year of uncertainty, where investment decisions are made in a vacuum of outdated standards and potentially, increased risk.
Lessons from the Offsite Sector
The offsite sector hasn’t had an easy ride, particularly in the midst of macroeconomic disruption – the Covid pandemic, materials cost increases and high interest rates. But the demand for new, energy-efficient homes has not gone away.
What has emerged is a new generation of offsite solutions – leaner, more focused, and better aligned to meeting the needs of both developers, homeowners and tenants. These requirements include genuine design flexibility – whether for market sale, build-to-rent or social housing – and cost parity with traditional housebuilding methodologies.
The TALO model is defined by a few key features that take learnings from Finland – dry processes from forest and sawmill to site to reduce snagging and improve air tightness; highly flexible yet repeatable design; a holistic approach that integrates the highly insulated building fabric, energy strategies, foundations and robust quality control. This combines to offer a route to compliance that de-risks project delivery and significantly improves outcomes for homeowners and residents.
With this model, the factory process is designed to minimise air permeability at each stage to a standard that is very difficult to achieve using traditional construction.
A recent TALO timber offsite project in Kent, for example, achieved air tightness levels in the first test of 0.46 m³/hr/m², significantly exceeding both Part L and Passivhaus requirements, whilst achieving cost parity with traditional construction.
Why the Future Homes Standard will Accelerate the Demand for Offsite
We believe the new standards will increase the pressure on traditional construction methods, particularly in terms of additional cost and the risk of non-compliance. Major housebuilders still reliant on out-dated techniques may find it increasingly difficult to achieve consistent results at scale.
Construction skills shortages further compound the situation. Simply put, the skills required to deliver ultra-low energy homes – notably air tightness – are not widely available on UK building sites. Offsite manufacturing addresses this by embedding those skills within the production process and by using highly trained, employed labour.
The housebuilding sector still has to address the reputational impact of persistent snagging and sub-standard quality issues. As regulatory standards are raised, the tolerance for poor performance will reduce. And as developers look for ways to build better, faster, and more reliably, we believe offsite manufacturing will become an increasingly attractive proposition and solution to reducing the risk of non-compliance.
Rethinking Energy Strategies: A Holistic Approach
One of the misconceptions around achieving compliance with the Future Homes Standard is that it will require costly systems such as air or ground source heat pumps. However, our view is a more effective and sustainable strategy begins with the building fabric itself.
A highly insulated, air-tight envelope manufactured to precision tolerances can radically reduce the need for costly solutions such as heat pumps. When combined with solar panels, battery storage, MVHR (mechanical ventilation with heat recovery), and electric underfloor heating, homes can comfortably exceed the new standards without additional cost. And energy bills will be driven down or even eliminated.
This is the strategy deployed by TALO’s customers, where energy costs are radically reduced by taking a holistic and more strategic approach where building performance and outcomes are built in at the outset – not bolted on with the addition of a heat pump.
Looking Ahead
The Future Homes Standard should not be the end goal. It should be the baseline – a prompt for deeper innovation and faster adoption of already proven methods.
For developers and housebuilders, the message is clear: the tools to build better homes already exist. The question is then not whether to meet the new standards, but whether there is the will to exceed it, before being required to do so.